Leah Grout-Garris |
January 1, 2013
An iconic building that started out as nothing more than a drawing on a cocktail napkin recently celebrated its 50-year anniversary. The 650-foot-tall Space Needle was completed in December 1961 and opened on the first day of Seattle’s World’s Fair in April 1962.
So what does it take to manage a high-rise fastened to a 30-foot-deep foundation with 72 30-foot bolts? Eleven dedicated facilities engineers who work around the clock to respond to building needs and carry out routine maintenance.
Facilities Manager J. Taylor has been employed at the Space Needle for eight years. His team focuses on three major goals:
- Maintaining the Space Needle to the highest integrity possible (and maintaining mechanical systems to factory specs).
- One-day turnaround time on almost all work orders.
- Safety for team members to prevent on-the-job accidents and lost time.
Keeping Up Appearances
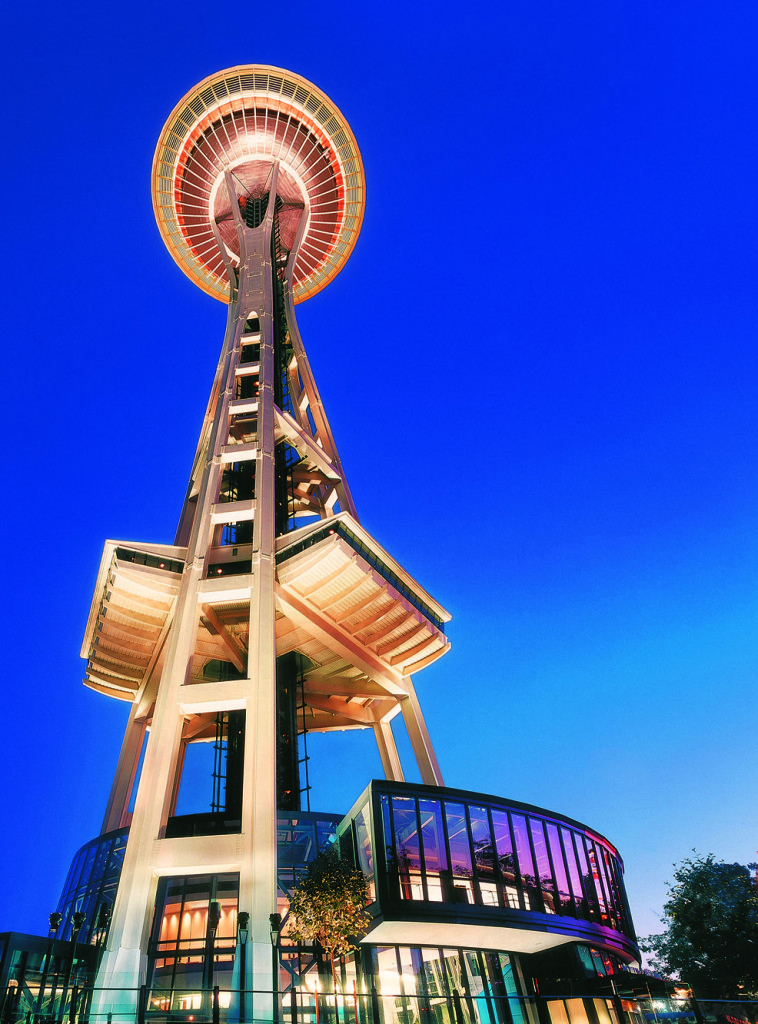
Built in 1962, the Space Needle is managed by 11 dedicated facilities engineers who work around the clock to address work orders and complete routine maintenance. From painting the roof a specific color for special events (like the Space Needle’s 50th anniversary this year) to supervising fireworks shows off the top of the structure, the facilities management team makes it happen.
To make sure the Space Needle looks good for tourists (and to prevent any inconveniences for them), Taylor says big facilities management projects are planned around peak season (summertime). “With the Space Needle’s hours of operation, it’s difficult to get work done when we have our tourists and guests around, so we do the majority of our work overnight through the staff members on our graveyard shift.”
It’s during these times that work is completed on systems affecting the tourist experience, such as the elevators. Because the Space Needle’s elevator hoistways are exposed to the elements, Taylor’s team focuses on maintenance to keep them running smoothly, but that’s tough to do when the elevators are running during the day. The size of the elevators presents challenges as well. “If a piece of equipment doesn’t fit inside that elevator, it has to be dismantled to fit,” says Taylor, “and then reassembled once it gets to where it’s going.” A lot of this work is done overnight.
Working on Work Orders
Taylor says the one-day turnaround time for work orders has made the facilities management team much more efficient in managing requests placed by the Space Needle’s 325 employees. “It’s much easier to follow up and track work order requests.”
Part of the team’s success is due to coaching, says Taylor. “I spend time with my staff to make sure they check for work orders regularly, and coach them on using the system and explaining the benefits.”
Previously, the team was having trouble tracking requests coming in via e-mail, phone, and even through word-of-mouth. “If I wasn’t part of the conversation, I wouldn’t know what was going on and couldn’t track it or provide updates,” says Taylor. “But getting employees to place work orders ensures that their requests can be followed up on by our team.”
Success with Sustainability
The Space Needle also focuses on green operations whenever possible. “Some of our best practices include upgrades to our lighting system. We’ve changed out to more energy-efficient, long-term lighting solutions so our lights don’t go out nearly as often. This also saves us time, because we don’t have to change them out nearly as often,” says Taylor. He says his team has used the time saved on lamp change-outs to focus on regular preventive maintenance for other mechanical equipment.
Not only has being sustainable helped the facilities management team save time and cut down on energy use, but Taylor says it’s also helping the organization keep costs down.
The Space Needle composts all of the food from its kitchen, including scraps and waste from food prep. “Not only is that good for the environment, but it also impacts our bottom line because we don’t pay to send it to the landfill,” explains Taylor. “We have a company that comes in and takes scraps away for free; they compost it and then use it.” The Space Needle also installed a triple water filter system to offer water to guests vs. serving bottled water. This eliminated purchasing costs, as well as the waste associated with bottled water.
Because the Space Needle is open to the public, Taylor says they keep cleaning chemicals and other substances to a minimum. “We want to make sure we’re environmentally friendly, and that our environment works for everybody.”
Saved by Facilities Management
“My building can be picked out just about anywhere,” says Taylor. “Because the building is so iconic, there are lots of great events going on year-round. And we get to be part of those events.” From celebrating the structure’s 50th anniversary to the fireworks show off the top of the Space Needle every New Year’s Eve, Taylor and his crew help make it happen.
Director of Marketing Mary Bacarella is responsible for the Space Needle’s event planning. “We come up with these ideas, but someone has to implement them,” she explains. “Whether it’s 4 a.m. and we need enough power to shoot a commercial, or we have to paint the roof a specific color in three days … facilities management figures it out.”
Taylor says his team balances these special events and requests with their regular workload, but his team members volunteer to do so. “They love being part of it, and it’s a great honor to be able to say, “I helped with that.’ ”
Leah Grout-Garris
An award winning editor, Leah spent over eight years in senior editorial positions at both BUILDINGS magazine and ARCHI-TECH magazine. Her work has been incorporated into training and educational programs around the country. She is a graduate of University of Iowa. She is Editor at Large for High Rise Facilities.
Tags: featured, Seattle
Category: Foundations, Seattle