The 18-story Byron G. Rogers Federal Building underwent a modernization project that brought energy usage down by 63 percent.
It’s always exciting when major green building projects are complete. But what really happens after they’re done? Do the MEP systems perform as planned? Are energy savings occurring at the level expected? Are tenants and occupants more comfortable?
For the Byron G. Rogers Federal Building modernization and renovation project, the answer is a resounding yes.
Located in Denver, Colorado, this 18-story, 494,156-square-foot facility is home to 11 federal agencies. Built in 1965, the building needed major upgrades, as well as a fresh approach to how the interior space was being used. “It was truly a 1960s building,” says Michelle Swanson, mechanical project engineer at The RMH Group. “There were private offices all around the perimeter. It was dark inside the building, with a lack of natural light. A few executive orders passed down through the government were aimed at reducing overall square footage for agencies, so several were moving toward open-office environments. We wanted to do something similar.”
When the American Recovery and Reinvestment Act (ARRA) rolled out in 2009, it gave the U.S. General Services Administration (GSA) an opportunity to invest in the Byron G. Rogers Federal Building infrastructure. “It’s sometimes difficult to get funding to improve our buildings, especially for major construction and renovation projects, so the ARRA was a perfect fit,” says Sally Mayberry, regional public affairs officer for the GSA. “It came at just the right time.”
As part of the American Recovery and Reinvestment Act, the GSA also needed to make the Byron G. Rogers Federal Building more sustainable. “That was a critical component of our mission: to not only improve the infrastructure, but also improve energy efficiency,” explains Bryan Zach, GSA project manager.
Prior to the start of any modernization or renovation work, the GSA conducted a feasibility study – a report on the age and life of the building systems. Many of the MEP systems were original to the 1960s building, so they were past their useful life. “A few chillers were replaced in the mid ‘90s, but we knew we could get more efficient chillers,” Swanson explains. So it was decided that most systems would be replaced in order to reap significant returns on sustainability investments and add 100 years of life to the aging building.
In 2010, the modernization and renovation project began, with several goals in mind:
- Improve energy efficiency and sustainability so the building could serve as a model for the GSA portfolio
- Turn an older real estate asset into a high-performing building
- Restore the historical aspects of the facility
- Create a healthier, more inviting work environment
“We were working with 1960s vintage construction,” says Swanson. “The insulation, windows, and mechanical systems all needed significant attention. So we ended up taking the building clear down to the skin from the inside – leaving the building skin for historical preservation purposes.” The building’s façade is an excellent representation of mid-20th-century Formalist style architecture.
To boost the bottom line, Xcel Energy was brought on board at the start of the project. The team developed an energy model based upon the sustainability technology selected for the building, and used the results of the model to determine the size of the rebate it would offer. “Xcel gave us a check for close to $350,000 in energy rebates,” Zach shares.
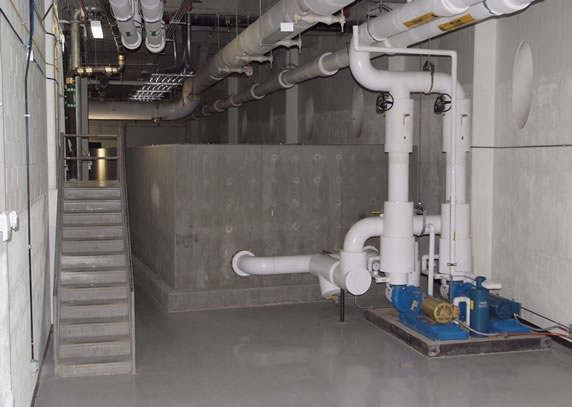
A 30,000-gallon water tank in the basement of the Byron G. Rogers Federal Building serves as a heat sink, storing heat during the day for release at night. (Credit: GSA)
Big Green Payoffs
Although the federal office building was vacated for the modernization, it’s connected to the courthouse – which remained occupied during the project. “Most of the courthouse’s MEP services are located in the federal office building, and had to be maintained during abatement, demolition, and construction of the space prior to cutting over the new services to the courthouse,” says Nancy Kristof, senior marketing communications manager at Mortenson.
Much of the green building technology considered for the project hadn’t been incorporated into other GSA facilities before. For example, the Byron G. Rogers Federal Building was one of the first buildings to be 100-percent LED lighting.
“We were actually trying to inform the market on LEDs,” says Swanson. “We met with different lighting manufacturers and explained that we had 18 floors of office space that required a lot of general office lighting, and asked them what they could come up with. We were looking at products that weren’t even on the market yet.” The LED lighting system is equipped with daylight harvesters; as the building receives more natural daylight, the LEDs dim accordingly. Occupancy sensors were also installed so occupants don’t have to worry about turning lights on and off.
To maximize daylight, induction units were removed from in front of windows, opening up nearly one-third of the nine-foot-tall glass panes. By placing mechanical systems overhead instead, the team was able to let in 25 percent more daylight through the windows – not to mention gain back floor space.
“Overall, people are amazed at how much natural daylight they have in the new building,” says Zach. “To take full advantage of daylight, we focused on placing open-office areas along the perimeter, and individual offices and other program areas requiring partitions in the interior. Tenants were excited about being able to see across the space and out the windows over downtown Denver.”
What replaced the window-blocking induction units was an active chilled beam system, which uses significantly less air than a traditional commercial HVAC system. “It relies more on water to heat and cool the space – there isn’t air blowing on you constantly,” Zach emphasizes. Offering even temperatures throughout the building, hot and cold calls have dropped significantly. “The number of hot and cold calls we receive here is also much lower than in other GSA buildings where we have standard mechanical systems in place.”
The building’s interior insulation was removed and the envelope was reinsulated. A new four-pane window system offers a super-thick thermal barrier that contributes to HVAC performance and improved thermal comfort throughout the space.
A 30,000-gallon water tank in the basement serves as a heat sink, storing heat during the day for release at night. The GSA can store enough to heat the entire building on a cold winter night – and an entire weekend – without turning on the gas boiler.
Submeters were also added throughout the facility. “Before, we were monitoring global energy use,” Zach explains. “Now we can monitor on a floor-by-floor basis, look at plug loads separately, examine lighting loads and HVAC loads on each and every floor, etc.” The GSA’s facilities management group analyzes that data and compares it to pre-modernization utility bills to see how much energy is being saved.
The goal was to reduce energy consumption by 55 percent beyond ASHRAE requirements, to less than 39.1 kBtu per square foot per year – and Zach says the building is right on target based on submeter data. The most recent figures from May 2015 indicate that energy usage is down 63 percent (a $423,000 savings) from pre-modernization levels. The building is also on track to save close to 40 percent in water use over the 2007 baseline, providing close to $20,000 in annual savings.
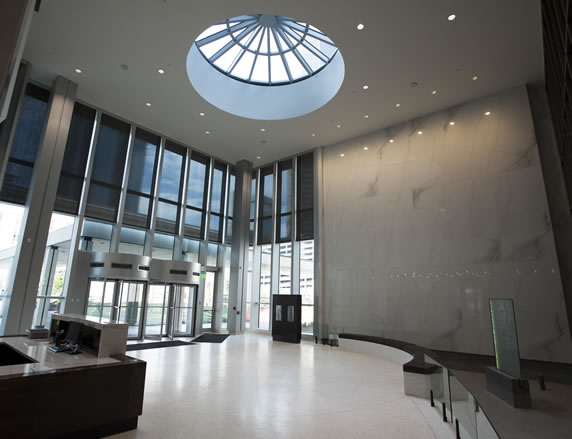
Working with 1960s vintage construction, the building’s insulation, windows, and mechanical systems all required significant attention. (Credit: GSA)
Improving the Interior
In the beginning, it was a challenge to get tenants to buy in to the fact that the new building was going to be better. “There were a lot of doubters,” says Zach. Once the building’s ground floor was completed, the GSA began to take tenants through the space. This helped raise excitement levels about the facility so tenants could look forward to moving back in.
Thanks to annual satisfaction surveys, the GSA already had a solid understanding of what the tenants disliked about their office space before the modernization began. Addressing the lack of daylight was a big priority, but so were amenities that would improve wellbeing, such as a fitness center, an in-house clinic for routine medical care, adjustable-height desks and walkstations, and a full-service cafeteria.
“I’ve worked in the Byron Rogers building for more than 20 years,” says Courtney Hoskins, aging services program specialist with the U.S. Department of Health and Human Services. “I wasn’t sure what to expect moving back into an old federal building. But I’ve been pleasantly surprised at how much I’ve been able to increase my overall wellbeing by taking advantage of the new gym, healthy food options in the cafeteria, and more natural daylight.”
GSA projects tend to drive the industry, says Zach, so whatever decisions are made ultimately impact private-sector construction. “We’re reducing energy, and coming up with creative and innovative designs, which is going to trickle down to the rest of the commercial buildings industry.”