Zeller Realty Group recently completed a build-out of 401 North Michigan’s top floor, retrofitting the space to include floor to ceiling windows. The 35th floor wasn’t designed to have a window wall system, but the team made it happen during one of Chicago’s harshest, coldest winters on record.
A classic Mies van der Rohe-style building, 401 North Michigan was designed by Skidmore, Owings & Merrill in the 1960s. Formerly known as the Equitable Building, the 35-story tower sits on the second largest plaza in Chicago. “Pioneer Court is second in size only to the Daley Plaza,” says Eric Taylor, assistant vice president at Zeller Realty Group. “The building purposely has a large plaza area so it could be set back from the road.”
The Chicago Tribune originally sold the land to Equitable Insurance Company; the purchase agreement required that the new building be set back so the historic Tribune Tower could still be seen from the south down Michigan Avenue.
Zeller Realty Group purchased the tower in 2001 from Equitable Insurance Company, which had built several similar towers across the country with very little variation in their architectural look and feel. The property is now 81 percent leased to tenants including Kraft, University of Chicago, MTV, and others.
401 North Michigan’s 35th floor offered a good starting point for a build-out: 10.5-foot ceilings, and an internal stairwell and shuttle elevator that connects floors 34 and 35. Zeller Realty Group
Buildings with this much history don’t often invest in noticeable changes to the exterior – the focus remains on building systems and efficiency upgrades. But Zeller Realty Group recently completed a build-out of 401 North Michigan’s top floor, retrofitting the space to include 10.5-foot-tall windows that stretch from floor to ceiling. Originally, the 35th floor didn’t feature any glass at all.
Moving From Paper to Practice
When Howard Meyer, Zeller Realty Group’s senior vice president of leasing, joined the company in February 2012, he discovered a number of great ideas for the 35th-floor space that had never been put into action. “There were drawings for the windows on the 35th floor, and a preliminary budget number, but the project hadn’t moved forward to get the space out in front of potential tenants.”
Meyer knew the build-out investment would be worthwhile: “If done right, this would be one of those unique spaces that would give you something to talk about with almost any tenant,” he explains.
The 35th floor offers 10.5-foot ceilings, and an internal stairwell and shuttle elevator that connects floors 34 and 35. “Those two floors almost had to go together because access to 35 is from 34,” says Taylor. On the east and west sides of the building was the original Equitable Insurance signage from the 1960s. Solid granite cladding around the perimeter served as the signage’s backdrop, with concrete block behind it. That architectural detail continued all the way around the top of the building.
There was only a flat roof above the 35th-floor space – no cooling towers or mechanical penthouses. Two-thirds of the 35th floor is mechanical room; the other one-third on the east side of the building is tenant space.
The team used swing stages for every bay they worked on during the 35th floor build-out. Any work done off the stages was delayed most of the winter. Zeller Realty Group
When initial talk of the 35th floor build-out began, a tenant was leasing both the 34th and 35th floors, using the top floor as a fitness center and conference area. Once the tenant vacated, however, Zeller was able to consider these big changes to the 35th floor. The plan of creating 10.5-foot-tall glass all along the east side of the building, and wrapping it around the north and south exterior walls, was under way.
Looking for a Leasee
“If I knew a broker who was in the market for in excess of 35,000 square feet, I wanted to talk to him,” Meyer explains. “Once the project was finished, I knew we could offer unique space with 10.5-foot clear ceilings, full-height glass, and the potential for operable windows. We wanted to create usable indoor-outdoor space.” While the project was in progress, Meyer planted some seeds by showing brokers and tenants the plans for the floor.
The leasing challenge, Meyer says, was the lack of direct elevator access. “We had to marry the 35th floor with the floor below, so we had to find a tenant who needed the 22,000 square feet on floor 34, as well as the 7,200 square feet on floor 35.”
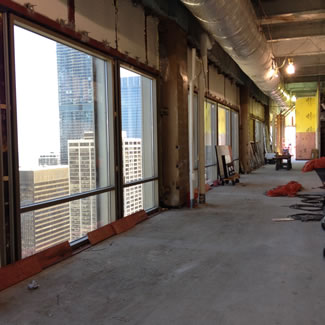
The lack of convectors on the 35th floor meant that window glass could start at the slab instead of two feet off the ground. Zeller Realty Group
At the time, Kraft CEO Tony Vernon happened to be looking for a “ ‘wow’ kind of space,” as Meyer describes. Vernon wanted a space to host company events, as well dedicated areas for Kraft University (which provides training for new employees and continuing education for existing employees) to use as well.
Preparing for Winter Work
“It’s always a challenge when you’re trying to retrofit something that wasn’t originally designed as part of the building,” says Taylor. “401 North Michigan’s 35th floor wasn’t designed to have a window wall system. But we worked a lot of those details through to make it happen.” And they did so during one of Chicago’s harshest, coldest winters on record.
After learning about Zeller Realty Group’s plans for the build-out, Kraft decided to sign a lease for both the 34th and 35th floors. Technically, says Taylor, it was the timeline that presented the biggest challenge – not the build-out itself: Making sure the 35th floor was complete by the time Kraft was ready to enter the space, even if it meant working through November, December, January, February, and March.
To accommodate snow, wind, and cold temperatures, Taylor built in four months of fluff time for weather delays. “We still met our schedule, but we used every day of the contingency because of extreme conditions,” Taylor explains. “We were able to do some of the work over the cold months, but not to the level that we would have liked.”
The top of the building was opened up in Fall 2013; the 35th floor was exposed to the elements all winter long. An interior wall set back from the curtainwall in-board was created as a temporary weather wall to keep the building weather-tight. The project also required waterproofing on the deck and over the open curtainwall exposed to the outside.
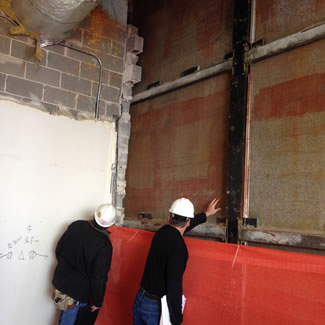
Exterior granite cladding, shown here from the inside after concrete block was removed, was removed and reinstalled to facilitate new steel and allow for waterproofing where the head of the new windows would be. Zeller Realty Group
“Because we had so much time to plan before we did the work – and we had so many eyes on it – we were able to create openings and look at existing conditions,” says Taylor. These inspections helped the team identify any underlying problems or challenges. Luckily, the assessment confirmed that existing conditions matched the building’s original drawings.
Work performed on the building envelope was done from a staging system on the roof. “We had swing stages for every bay we were working on,” says Taylor. Any work done off the stages was delayed most of the winter.
To protect exposed piping along the perimeter of the building, the team used temporary heat tracing and kept water circulating 24/7 to prevent freezing or bursting.
Some of the building’s existing granite cladding was removed and reinstalled to facilitate new steel and allow for waterproofing and flashing where the head of the new windows would be. “We were able to put the steel in during the winter, but until the weather broke, we weren’t able to put the granite cladding back on. All the window framing and glass were installed from the inside,” says Taylor.
While weather was the biggest obstacle, building out the 35th floor with tenants on the other floors wasn’t an easy task, either. The team isolated the potential for stack effect by building a temporary wall and door in the stairwell leading to the roof. “You take the tower stairs and go all the way up, and then you go through the roof hatch, so it became like a chimney,” Taylor explains. “To get past that, we had to put a door and wall up there to close it off, essentially bulk heading the top of the stairs.”
Any noisy curtainwall work – steelwork, anchoring plates, attaching steel reinforcement to standing beams and back to the columns – was done from 5am to 8am on weekday mornings, or on Saturdays.
An interior wall, set back from the curtainwall, was created as a temporary barrier to protect the 35th floor from the Chicago winter. Zeller Realty Group
What the Retrofit Brings to the Tower
The 35th-floor now offers several big “wow factors,” emphasizes Meyer. By engineering a new overhead variable air volume (VAV) system into the space, tenants have full use of the real estate without losing space at the perimeter like in a normal office with a base heating element. The lack of convectors on the 35th floor also meant that glass could start at the slab instead of two feet off the ground. “When you walk into that space, there’s view everywhere,” says Meyer.
An operable wall system, part of the southeast bay, provides the indoor/outdoor space the team envisioned. “All the other windows are fixed, floor-to-ceiling, 10.5-foot-foot high glass,” says Taylor. But in this terrace space, a NanaWall system is installed above 54-inch, solid glass. “It acts like accordion glass doors that fold to each side,” explains Taylor. “You can open an entire bay from 54 inches up to 10.5 feet; the fixed glass at the bottom becomes a solid handrail.” An interior wall constructed and weatherproofed like an exterior wall separates the terrace area from the rest of the 35th floor.
The 35th floor now offers view of the Chicago River and Lake Michigan, along with operable walls that create indoor-outdoor space. Zeller Realty Group
The new VAV system replaces an older, undersized system, and serves only the 35th floor. New controls and dampers are designed to condition the terrace space when operable windows are closed. When the windows are open, however, that area dampers off so humidity isn’t introduced into the rest of the space. Waterproofing was put down on the floor in the terrace area, along with a floor drain. If a tenant accidentally leaves the operable windows open during inclement weather, the terrace floor is designed to also act as a roof over the 34th floor.
“We essentially repurposed a windowless box to do what any developer would do: to get the highest and best use possible from the space,” explains Meyer. With this project successfully complete, Zeller is now looking into the possibility of moveable or operable windows elsewhere in 401 Michigan Avenue.
“People get excited at the prospect of unique space. When buildings can create an outdoor common area space, or offer a connection to the outdoors, we’re trying to do it. We want to create that unique marketing twist.”
Leah Grout-Garris
An award winning editor, Leah spent over eight years in senior
editorial positions at both BUILDINGS magazine and ARCHI-TECH
magazine. Her work has been incorporated into training and
educational programs around the country. She is a graduate of
University of Iowa. She is Editor at Large for High Rise Facilities.