With 48 stories and 1.4 million square feet, the Duke Energy Center (DEC) is a dramatic addition to the skyline of Charlotte, North Carolina. The tower opened in December 2010, and has become a leading model for energy efficiency and sustainability in the nation. It is currently the tallest office building, and the only building in the state of North Carolina, to achieve LEED Platinum Core & Shell 2.0 certification, the highest level awarded by the U.S. Green Building Council for Leadership in Energy and Environmental Design.
Duke Energy Center’s owners wanted the tower to be one of the most intelligent and environmentally friendly office buildings in the country. From the start, DEC was designed and built to meet the highest standards of energy efficiency and sustainability.
The inclusion of a 2.25-megawatt, seven-story data center which requires the highest levels of reliability, backup and redundancy was another priority for the DEC tower. The data center includes four floors for stock trading and presents its own set of challenges in terms of climate control, energy usage, security and reliability. Because a failure of any duration can have serious consequences for building tenants and their customers, data center up-time and reliability are critical.
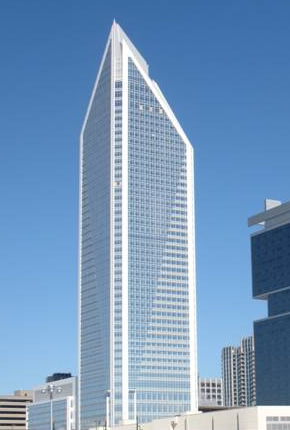
The Duke Energy Center uses advanced building technologies to create operational efficiencies that reduce energy consumption, promote sustainability and increase occupant productivity.
To achieve the aggressive performance and green goals set for the DEC, the building designers realized that they would need a sophisticated building automation system that could integrate, control and monitor the diverse equipment and systems that were essential for the comfort, safety and security of the building occupants.
Automation Solution
The designers and owners of the DEC tower needed an experienced building systems solutions provider to help them meet the challenges of integrating and controlling the many systems in the building. They chose a building automation system (BAS) that provided the best solution for integrating the critical building systems and equipment on a single platform. The BAS they specified works with multiple system protocols including BACnet, Lonworks, OPC and MODbus and can be integrated with equipment and systems from a wide range of manufacturers. Overall, the BAS offered the flexibility and centralized control that was needed to support the building’s LEED and efficiency goals.
The BAS runs on a redundant fiber backbone and monitors the building via a routed IP network. The system integrates, monitors and controls all major building systems and sub-systems including HVAC, energy, lighting, access control, water meters, electrical submetering, irrigation and water harvesting and elevators. To help optimize building performance, the BAS automatically aggregates, analyzes and archives data from these integrated systems.
The system’s functionality enables DEC engineers to coordinate multiple building systems, platforms and protocols from a single, centralized command center that delivers improved data management and centralized facility control. The need for staff training on the system has been reduced and monitoring processes and procedures have been streamlined, reducing the potential for missed alarms and improving response times. Duke Energy Center’s system continuously monitors building systems and energy consumption. Sensors and meters throughout the building constantly relay data to the system as well.
The BAS has also been integrated with the local electric utility which makes it possible to monitor usage by individual systems – including plug load, HVAC and lighting – floor by floor, down to the individual tenant DEC level. Demand control ventilation is used in all tenant spaces in the building. A Tenant Override System has been implemented that provides enhanced occupant comfort via an easy-to-use website dashboard that tenants can use to make after-hours HVAC requests.
Additional energy savings were achieved by using Start Stop Time Optimization throughout the facility. Sensors throughout the building gauge CO2 levels and send signals to the BAS workstation which directs the ventilation system to bring in fresh air based on occupancy and CO2 levels. Sensors in the parking structure that are connected to the system measure carbon monoxide (CO) levels.
Exhaust air is purged and fresh air is brought in when CO setpoints are reached in the parking garage. Redundant cluster servers with heartbeat monitoring technology constantly monitor the data center’s critical systems and offer the ability to automatically switch to backup in the event of a primary failure. The HVAC system for the data center has been optimized with demand control ventilation and underfloor air distribution that provides greater flexibility for controlling temperatures and reduces energy costs. A Cooling Plant Optimization Package was also added for the data center mechanical plant.
“In a facility like this, there has to be a lot of emphasis on control systems. They are essentially our eyes in the field, so that we can see what our tenants need and take the right actions,” says Ron Roach, chief engineer for Childress Klein Properties, the building management company for the Duke Energy Center.
The Duke Energy Center uses advanced building technologies to create operational efficiencies that reduce energy consumption, promote sustainability and increase occupant productivity. Duke’s BAS solution features dashboards and analytics that aggregate and analyze building data to drive energy reductions and cost savings. Daily tasks have been automated and building systems automatically adjust to conserve energy.
The Duke Energy Center has already seen significant results in the areas of sustainability that include:
- Achieving LEED Platinum for Core and Shell certification.
- Achieving energy efficiency that is 22 percent greater than a traditionally built tower of comparable size. This has saved DEC approximately five million kilowatt hours of electricity per year.
- Integration and monitoring of 480,000 gallons of harvested groundwater, rainwater and gray water. This has reduced costs and helped DEC save 30 million gallons of water a year.
Duke Energy Center continues to work with the local electric utility provider to further integrate its BAS with the utility’s smart grid technology for future load shedding capabilities and demand optimization.
Photo Credit: Duke Energy Center
Dave Hopping
Dave Hopping is Vice President and Business Unit Lead for Siemens Building Technologies Division.