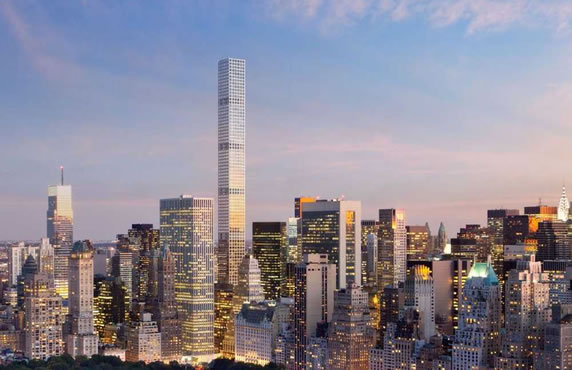
The biggest threat specific to Manhattan’s 432 Park Avenue project is water seepage. Engineers had to find a sealer capable of penetrating beyond 1” into the high density 14,000 psi architecturally reinforced concrete columns & spandrels. (Renderings: DBOX for CIM Group)
Standing at 1,397′ 432 Park Avenue is now the tallest residential building in the western hemisphere & truly is a spectacular feat of design, engineering & construction - the sheer size of the tower required over 70,000 cubic yards of concrete & 12,500 tons of rebar.
On a remarkably clear day, while driving across the Tappan Zee Bridge traveling from Connecticut to New York, if you happen to look to your left you’ll see the famous skyline of New York City approximately thirty miles to the south.
Easily picked out is the Empire State Building among the rest of the city’s famed landmarks. However, there is a new sight to see: 432 Park Avenue. The building itself rises strikingly, towering over a city famed for its skyscrapers. In fact, one might be hard-pressed to notice the rest of the skyline in the short drive over the bridge, transfixed by the incredibly tall, thin building, majestic in its height and lofty in its vision.
432 Park Avenue is a residential building filled with penthouses and apartments catering to those interested in the building’s prestige, location, and breathtaking views from the top floors. At almost 1,400 feet in height, the building is now the tallest residential building in the Western Hemisphere, a title made all the more impressive because of its lithe appearance.
The physicality of the building seemingly defies logic. Harry B. Maclowe, the project’s developer, and the construction teams created a marvel of architecture and engineering. For such a tall building to occupy such a small footprint of 33,000 square feet is nigh unheard of. However, thanks to such brilliant ideas as creating an ingenious system of balances and counterbalances, as well as periodic open spaces designed to let wind blow through the tower itself, 432 Park Avenue is safe and solidly built.
Completely poured in place, consisting of high-density 14,000 psi reinforced concrete, the building is one of the strongest and most durable ever constructed, likely to dominate the New York City skyline for generations, however, the project’s engineers worried about the effect of weather on the concrete.
The degrading effect of weather is exacerbated by water and chloride salt ingress, both of which are found in abundance in New York City, as it is located on the ocean. If chloride salt via chloride ion ingress and water make their way through the permeable surface of concrete, they will wreak havoc inside the substrate, slowly ruining the structural integrity of the concrete, corroding the steel reinforcements within.
How, then, was the construction team to defend against the untiring and unceasing force of nature? First of all, the concrete was created and poured to the density of 14,000 psi, as noted earlier. The high density means it takes longer for water and chloride salts to enter the concrete substrate. However, permeation is still bound to happen eventually.
Concrete’s strength lies in such permeability, as it allows the exit of gases and liquid that gradually strengthens the material over time. What makes concrete stronger is also its Achilles’s heel: as gases can exit, water and chloride salts can enter. No amount of density will stop this process.
The biggest threat specific to the 432 Park Avenue project is water seepage. The concrete, which is chemically highly alkaline, passivates the steel, allowing it to remain uncorroded. However, water carrying salt, which is very common in coastal regions such as New York City, would insidiously make its way into the concrete. Once inside, the salt would corrode the steel reinforcements by dissolving the concrete’s passivating layer, leading to rusting. The rusting, in turn, would degrade the concrete’s internal structure, leading to a variety of problems, all of which would be invisible to the outside eye. Known in the scientific and construction communities as “chloride-induced corrosion,” it would spell disaster for the building, and could ultimately render it uninhabitable.
In order to prevent the deterioration of the building and simultaneously maintain the white architectural aesthetics of the modern exposed concrete, the 432 Park Avenue engineers decided to treat the concrete with a clear sealer. These products, coming in a variety of forms and chemical make-ups can offer such benefits as water repellency but more importantly the ability to aide in a dramatic reduction of chloride-ion ingress, all while still allowing the natural movement of gases so essential to concrete’s strength.
As the engineers embarked upon the daunting task of evaluating and comparing sealers, they soon found out, however, not all products offer the same level of protection, nor do they all even repel water and salt while allowing such permeability. Many sealers will lock out moisture, but also will not allow the flow of gas out, which essentially ruins the material for its primary purpose of strength and durability.
The best type of sealer for 432 Park Avenue’s specific situation is a clear penetrating silane sealer. Silanes create a network of water-repellent, yet water-vapor permeable, silicone resins. These resins lock out water and salt, all while allowing the concrete to “breathe,” exhaling excess water vapor over the length of its life.
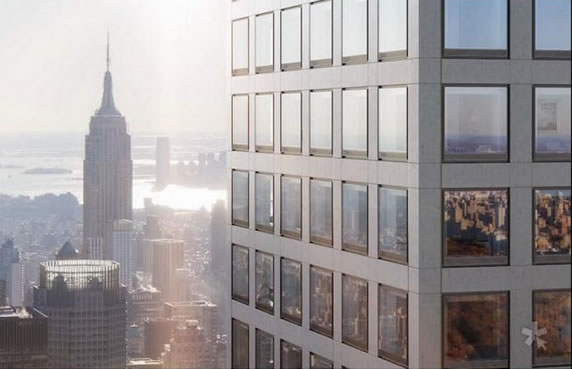
Standing at 1,397′ 432 Park Avenue is now the tallest residential building in the western hemisphere & truly is a spectacular feat of design, engineering & construction - the sheer size of the tower required over 70,000 cubic yards of concrete & 12,500 tons of rebar.
Accordingly, the team contacted the most reputable companies that produce silane sealers to test their products. For most types of concrete, a typical silane sealer will easily penetrate the porous substrate but for a vertical application poured to such a high density as at 432 Park Avenue, the engineers soon found that there was a consumption dilemma: the concrete sealing products would drip down and partially evaporate off the vertical surface of the building before penetrating within the substrate to the level necessary to provide lasting protection.
Searching for an alternative, the engineers contacted KreteTek Industries, the manufacturer of the Ghostshield line of concrete sealers. The company had recently developed a new type of silane sealer that featured a far higher viscosity than the average silane concrete sealer, which rendered it highly well suited to vertical applications on dense concrete: the 432 Park Avenue engineers had found their solution.
In side-by-side core tests of KreteTek’s Iso-Tek 8501 versus traditional silane sealers conducted by the team’s engineers, the KreteTek product penetrated well over an inch into the concrete substrate after only two coatings, a previously unheard of feat for such high-density concrete. Compared to the results attained by its competition, the Iso-Tek 8501 was the only choice for the 432 Park Avenue construction team.
The sealer protects concrete through a form of hydrophobic impregnation, penetrating within the concrete substrate to form stable covalent bonds between the silane in the sealer and the pores and capillaries in the concrete. It permeates the substrate while simultaneously resisting the naturally high alkalinity of the concrete. This allows it to function as a chloride barrier, repelling water and its attendant salts from entering the concrete and degrading the steel reinforcements.
As a water-based silane sealer, the Iso-Tek 8501 is about as environmentally friendly as concrete sealers get, while also offering a relatively easy application process. The high viscosity of the sealer allowed the application crews to control the consumption rate of the sealer into the concrete substrate. Solving the consumption dilemma faced by the 432 Park Avenue engineers reduced waste from dripping and evaporation, which led to a reduction in layers and total product utilized all while increasing the product’s long-term reliability.
Applicators recently finished coating the entirety of 432 Park Avenue’s exterior by hand, a truly massive and ambitious undertaking. The structure will now stand protected from water and salt well into the future, granting developers, insurers, and residents an indefinite peace of mind.