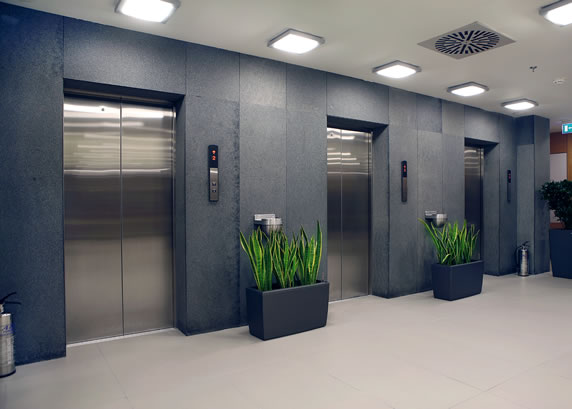
Elevator commissioning is a crucial safety precaution, serves as a means of due diligence, and ensures compliance.
The Commissioning Process Explained
Elevator commissioning is a broad, systematic review of the system to ensure that all mechanisms are performing as designed. It’s considered a “building lifecycle” process that involves setting initial parameters in the planning phase, followed by regular testing conducted through design and completion of the building. The process is then supported long-term through recurring system re-testing after occupancy.
The process of commissioning should not be confused with a basic equipment check. This is a much more detailed process that involves utilizing an experienced commissioning agent to conduct overall system diagnostic testing to make certain everything is working properly, and then providing a detailed analysis report to building ownership.
During the early commissioning phase, a checklist of specified performance requirements is developed for crucial performance areas, including:
- Acceleration and deceleration rates
- Elevator capacity
- General ride quality
- Door times
- Decibel levels to measure sound quality
As the building approaches final occupancy, a complete performance audit of the entire system is conducted once again. Snapshot tests are then carried out every few years to make sure all systems are running smoothly.
Reasons to Consider Comissioning
Elevator commissioning is a crucial safety precaution. Case in point: During a recent, routine audit of building equipment to uncover possible code violations, a commissioning team also checked the condition of the elevator hoist ropes. This inspection revealed that a six-inch section of rope had rusted and broken out; the problem was immediately communicated to building ownership. Discovering and repairing this critical flaw helped prevent a potential disaster.
Long-term commissioning also helps elevator systems stay compliant with state-mandated code requirements, which include additional requirements like fire recall operation, earthquake protection, and standby power. State or other jurisdiction is initially responsible for setting the ground rules; building designers and construction professionals are tasked with incorporating these requirements into the design documents and installing systems accordingly. Elevator commissioning can confirm that the intent from the documents and required performance is met, and that all specified equipment has been properly installed.
Commissioning serves as a means of due diligence to save money long-term, too. Owning and operating a building requires a substantial financial investment; poor elevator performance can result in excessive repair and replacement costs, as well as tenant complaints. Building commissioning will help prevent this unnecessary financial loss by keeping equipment and building systems at their highest level of performance.
Commissioning also plays a role in enhancing energy efficiency, another potential area for cost savings. Today’s properly designed and commissioned elevators include systems that conserve power in a number of ways, including shutting down system lights and fans when not in use.
Getting Started
Typically, a building owner directly contracts with an independent third-party commissioning agent for this type of project. While there is no licensing required for elevator commissioning, certifications exist that can make a building owner feel more at ease in knowing they’re working with an experienced professional. For example, Qualified Elevator Inspection (QEI) certification ensures that inspectors are intimately familiar with the elevator code and are trained in commissioning new equipment installations, repairs, alterations, or maintenance of elevators or related equipment.
Elevator commissioning provides a building owner with an unbiased, objective opinion of the overall systems, which ensures that standards and specifications are met – and even exceeded.
Photo courtesy of Syska Hennessy Group
John Moran
John Moran is a senior vice president with the Syska Hennessey Group San Francisco office, and has been with the company for almost three decades.