To keep up with guest demand, high-rise hotels invest in plumbing, elevators, and HVAC systems – and technology that allows for custom control.
Comparing high-rise hotels with low-rise suburban hotels – especially when it comes to MEP systems (mechanical, electrical and plumbing) – won’t get you very far if you’re looking for ways to preserve operating costs while keeping guests comfortable. Some energy-efficiency measures, such as LEDs and window film, can be applied across the board for hotel savings. But, in many cases, conservation strategies that are successfully implemented in a suburban hotel are completely different than those that will work in a hotel tower.
For one, high-rise hotels tend to have greater occupancy rates, says Glumac President Steve Straus – and they often have more than one person staying in each room. That translates to good news for energy-efficiency projects: The amount of energy intensity from a high-rise hotel’s MEP systems make more expensive energy-efficiency investments possible because they provide a much quicker payback.
“For example,” explains Straus, “a heat reclaim system for the domestic hot water in a suburban hotel would never pay for itself because you’ve got one person in each room taking a quick shower in the morning. But these systems would pay for themselves in a high-rise hotel when there are two or three occupants in a room, and showers are being taken in the morning, in the early evening, and late into the night.”
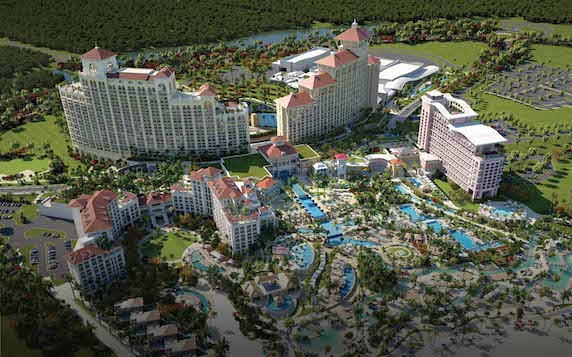
Located in Bahamas, Baha Mar is said to be the western hemisphere’s largest current resort project, and is teaching some valuable lessons in vertical transportation for high-rise hotels.
Here’s what’s happening with the MEP systems in high-rise hotels across the country, as facilities professionals make investments to save energy and keep guests satisfied.
More than Just a Pretty Interface
Millennials are impacting everything in hotels – right down to the MEP systems. “In the next 10 to 15 years, more than half of the people staying in high-rise hotels will be Millennials,” says Craig Watts, principal/vice president and director of corporate market development for MKK Consulting Engineers. They’re savvier when it comes to technology, and they want to be able to control things themselves – including the space they’re staying in – through their phones.
To make sure the controls are used properly, the interface needs to have graphics that are large and easy to understand. “If they’re small and complex, and people can’t read them, this individual control will actually cause more harm than good,” says Straus, “with lots of complaints and unnecessary maintenance calls.” Your maintenance team may spend a large amount of time simply trying to describe the controls to guests if they aren’t self-explanatory.
One of Watts’ recent hotel MEP projects involved a hospitality learning center in Denver (a hotel operated by students who want to learn the ins and outs of hotel management). His team installed a system that allowed all guestrooms to be controlled from the front desk. Instead of relying on maids to remember to reset each room, they can all be centrally controlled. When a guest checks in, the front desk employees turn on the fan coil, turn up the lights, and set whatever mood they’d like in the room. If the guest is checking out, employees can move the room into “unoccupied mode,” which turns off heating and cooling, lighting, electronics, etc.
An MEP trend that began in Europe is starting to move into the United States and impact hotel MEP systems as well, says Watts. “Some high-rise hotels now require us to install a master kill switch. With the push of one button inside the room, you can kill all of the electrical that doesn’t need to be on.” This prevents guests from having to manually turn off the lights, turn down cooling, etc. before they leave.
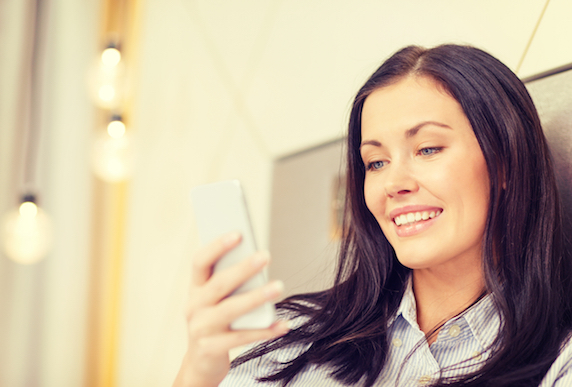
Millennials are savvier when it comes to technology, and they want to be able to control things themselves – including the space they’re staying in – through their phones.
Watts has discovered, however, that two electrical systems may be necessary to make kill switches a success. “Sometimes guests may be leaving the room for a while, but they want some power left on to charge their iPads or their laptops,” he explains. In these cases, color-coded outlets can help indicate which will be left on even if a kill switch is pushed.
Heating Up & Cooling Down
If your hotel is scheduled to undergo an interior refresh anytime soon (repainting, replacing carpet, etc.), Straus says it’s a good time to investigate the possibility of servicing fan coil units and retrofitting them with ECM motors.
Offering between 85% and 90% efficiency (as compared to the motors originally provided in fan coils that were only 40% to 45% efficient), this trend is catching on – and is one of the most significant (and simplest) energy retrofits that can be done for existing hotel facilities. “No one used to evaluate the efficiency of the motors in fan coil units,” says Straus. “But if you’ve got 1,000 rooms, it really adds up to a big load.”
Straus likes to design the ECM motors with three adjustable settings. Once the three pre-determined set points are specified, the motor is shipped from the factory with those modifications. When the ECM motor is at a high speed, it’s a little noisy by design so it can be heard. “Oftentimes, when people switch their room to full cooling, it’s because they want to hear that fan run,” Straus points out. Medium speed is designed to be barely audible; low speed can’t be heard at all.
VRF (variable refrigerant flow) systems – often found in offices – are becoming popular in high-rise hotels, too. They provide localized or zoned heating and cooling vs. distributing heating and cooling up and down through the entire building, Watts explains. By operating at varying speeds, VRF units work only at the needed rate, allowing for substantial energy savings in partial-load conditions. Heat recovery VRF technology allows individual indoor units to heat or cool, while the compressor load benefits from internal heat recovery. The system can control the amount of refrigerant flowing to each of the evaporators, enabling the use of several evaporators that offer different capacities and configurations, as well as individualized control, simultaneous heating and cooling, and heat recovery from one zone to another.
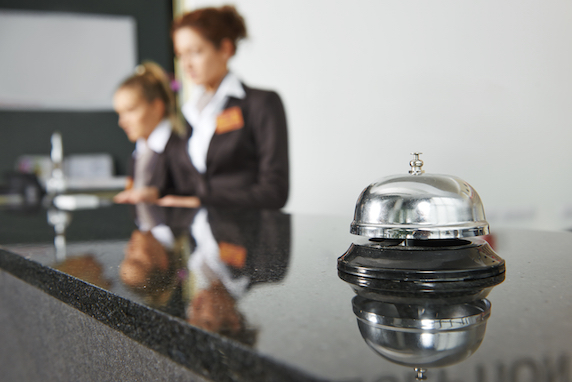
Modern controls can allow guestrooms to be controlled from the front desk. When a guest checks in, the front desk employees turn on the fan coil, turn up the lights, and set whatever mood they’d like in the room.
“In a high-rise hotel with an east-/west-facing exposure, you can really save a lot of money when one side swaps energy with the other,” Watts emphasizes. In the morning, for example, the east side of the hotel is likely being warmed but the west side is still cold. In these situations, VRF systems would allow the hotel to use energy being heated up on the east side and pull it over to the west side for warmth. In fact, Watts is seeing energy savings of between 30% and 35% when using VRF systems.
Straus shares one note of caution regarding VRFs, however: “These systems have a lot of refrigerant in them. If there is a leak in a hotel room, it could displace all the oxygen and kill a guest.” Completing refrigerant calculations (involving the maximum amount of refrigerant in the circuit, and the smallest room sizes) to determine whether a leak could cause death is vital. “In locations that are subject to earthquakes, the potential for refrigerant leak in the piping system is more significant.”
Going with the Flow
In most facilities, low-flow plumbing fixtures receive a lot of praise for contributing to significant water savings. But these common fixtures can cause problems in high-rise buildings, including hotels. “In older buildings, waste lines were originally installed with a slope at a modest angle,” Straus explains. “That was before low-flow fixtures were developed, and there was plenty of water to flush solids. Installing low-flow fixtures in these buildings can plug up the lines because they’re not sloped at an appropriate level.”
It can turn into a real maintenance nightmare, Straus warns, and cause build-up and back-ups due to decreased water flow (and, as a result, a reduction in the effective transportation of solids through waste lines). Investigate your existing infrastructure before assuming that existing fixtures can be replaced with low-flow models without any consequences.
Low-flow faucets may also lead to less hot water flowing through the building’s pipes, which can cause water waste when guests have to wait for the hot water to reach their faucets or showerheads.
Having an expert available to address and troubleshoot elevator problems immediately can help prevent problems from turning into major mechanical issues. With the size of Baha Mar, an elevator mechanic is onsite for 14 hours every day of the week.
Taking Guests for a Ride
Elevators are also getting a closer look at many high-rise hotels. Baha Mar, a mega resort located along Nassau’s Cable Beach in the Bahamas, is said to be the western hemisphere’s largest current resort project – and is also teaching some valuable lessons in vertical transportation for high-rise hotels. Procurement, installation, and turnover of the elevators for this project are being executed by the ThyssenKrupp Elevator Miami office operating in the Bahamas. ThyssenKrupp Elevadores SA (ThyssenKrupp’s Latin America regional office) will maintain the facility’s elevators after installation and turnover are complete.
The $3.5 billion resort offers 2,200 hotel rooms, and involved installation of 76 elevators (one pre-engineered hydraulic, two engineered hydraulic, one freight hydraulic, one residential elevator, two wheelchair lifts, eight escalators, and 61 traction elevators), along with eight escalators. Christophe Sailly, director of sales and business development for ThyssenKrupp Elevadores, says that a trend at Baha Mar to improve first impressions involved customizing elevator cab interiors. “Each hotel, including Rosewood, Grand Hyatt, SLS Lux, and the 25-story Baha Mar Casino & Hotel, wanted its own design to mesh with the overall feel each one was trying to portray.”
He says that a few large panoramic elevators were also installed, which allows the resort experience to continue as guests travel to and from their destinations. This is just one more way to impress and amaze guests in hopes that they return to Baha Mar.
In high-rise hotels, Sailly says, it’s vital to select the right type of elevator for each application inside the building. “For example, most of the elevators at Baha Mar are MRL (machine room-less), but we also have a lot of the gearless traction elevators to provide quicker floor-to-floor times.” These gearless solutions also save up to 25% over the industry average for every kilowatt used to power the elevators. Sailly’s team also installed 10,000-pound freight elevators to bring up equipment as needed.
With such a large number of elevators on the resort, selecting the right elevator for each application was only one of the challenges. The other involves having an onsite resident elevator mechanic available once the project is complete. Depending on the level of guest service your hotel is expected to provide, having an expert available to address and troubleshoot elevator problems immediately can help maintain guest satisfaction levels and prevent problems from turning into major mechanical issues. “We will have someone there seven days a week, 14 hours a day,” says Sailly. This vertical transportation team will also perform the weekly and daily routine maintenance required to keep elevators performing to their maximum once the buildings turn over and receive a certificate of occupancy later this year.
MEP systems are a critical element in any new or existing high-rise hotel. Not only do these systems determine utility bills and water/energy usage, but they also influence guests’ impressions and comfort levels. Your hotel’s furniture may be comfortable, and the artwork may be impressive, but if noise, temperature, humidity, water quality, or lighting control interferes with the guest experience, that’s the experience that will most likely be remembered.