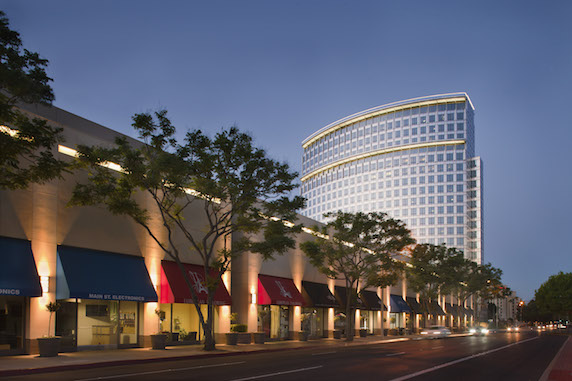
Plaza Tower, a 21-story, 470,000-square-foot tower, is the first multi-tenant building to achieve LEED-EB: O&M Platinum certification in Orange County, California as of January 2015.
The 21-story Plaza Tower in Orange County continues to improve energy and water efficiency while keeping tenants satisfied
Of the 100+ Class-A office towers that skim Orange County’s skyline, there are a handful that stand out for their quality construction and tenant amenities. These buildings attract high-end tenants like IBM, Subaru of America, and law firms from the Am Law 100 list (in fact, 70 percent of the law firms listed are tenants in one of four Orange County towers). Not only do these existing buildings have to go up against new construction in the area, such as the 21-story 520 Newport Center, but they also have to compete against each other to stand out.
Plaza Tower, a 21-story, 470,000-square-foot tower, is the first multi-tenant building to achieve LEED-EB: O&M Platinum certification in Orange County as of January 2015. As one of three buildings that make up the 1.2 million-square-foot South Coast Plaza, Plaza Tower is part of South Coast Plaza’s commitment to reducing CO2 emissions by more than 9.5 million pounds annually and reducing water consumption by over 3 million gallons annually.
In 2009, after being one of the first buildings in the country to achieve LEED-EB: O&M Gold, the Plaza Tower management team was invited to Washington, D.C. – along with the U.S. Green Building Council’s Rick Fedrizzi and White House Council Chair on Environmental Quality Nancy Sutley – to present their findings to Henry T. Segerstrom on the best methods for approaching LEED. Segerstrom was a visionary real estate developer in Southern California, and helped develop the first air-conditioned office tower in Orange County.
“We needed to improve the efficiency of the building without having anything other than a positive impact on our tenants,” explains Stan Taeger, who led the building’s LEED certification process as director of office property management for South Coast Plaza. “There are ways to cut energy and water that actually make tenants less comfortable and reduce visual acuity, but we will not accept that.”
As a result, the team decided to skip over some common green building practices, such as day cleaning, due to the fact that they may be disruptive or cause discomfort for tenants. “We didn’t slash things to get to LEED Platinum,” Taeger explains. “We did it in a way that enhances the environment as opposed to subtracting from the environment.” The team has achieved 82 of the 110 points possible in the LEED green building rating system.
Here’s a glimpse at what Plaza Tower has done so far to maximize building performance and contribute to better facility operations – all while keeping tenant comfort and efficiency top-of-mind.
Building-Design Breakthroughs
Efficiency is somewhat inherent to Plaza Tower due to Cesar Pelli’s building design, explains Taeger. “We’ve always been a 95+ ENERGY STAR building.”
The tower’s linen stainless steel finish is designed to “glow” vs. reflect in natural sunlight. Reflections are diffused by a nearly invisible pattern that has been stamped onto the building’s stainless steel panels, eliminating hotspots. The roof is made of a lightweight concrete with a high-performance coating to improve insulation.
To reduce dark spots at night and improve tenant safety, the Plaza Tower parking structure doesn’t have any shear walls, says Rob Lambert, director at Cushman & Wakefield of California. The building’s central plants are located in the base of the parking structure, using up this less desirable space for building systems in order to create more leasable square footage within the tower itself. The garage also offers eight vehicle charging stations for tenants to use.
Optimizing MEP Systems
LEED-EB: O&M certification often comes down to a building’s mechanical, electrical, and plumbing systems: As the systems that consume energy within the built environment, these systems also directly impact tenant well-being and productivity. Engineering MEP systems to achieve energy savings and tenant comfort requirements can be a delicate balance.
[pullquote]When you get into the Plaza Tower elevators, you can stand a nickel up on its end, ride up to the top floor and back down, and the nickel won’t fall over.[/pullquote]During the design phase, the Plaza Tower team decided to incorporate a larger outside air shaft, which allows the building to use outside air capacity vs. pure chiller air for additional cooling or initial building cool downs. “In the Orange County area, we’re kind of in a micro-climate as opposed to the general ASHRAE building profile for the area,” explains Taeger. “We get a lot of very cool mornings, even though it might get up to the mid-70s or even 80s. We can use that cool outside air capacity to help significantly reduce the building’s energy usage.” But when chillers are required, the tower’s HVAC system is comprised of chillers in three different sizes to optimize load; the team has also installed variable frequency drives and other technology to improve efficiency.
Holidays often result in HVAC energy waste for the average high-rise office, but Plaza Tower minimizes this problem by surveying tenants beforehand to find out who will be in the building – especially on “semi-holidays,” as Taeger refers to them: Memorial Day, July 4 and July 5, and Labor Day. “We allow the tenants who will be open to call in for air-conditioning only if they decide to work as opposed to having the HVAC running all day.”
Almost all of the common area lighting has been retrofitted with LEDs. “The quality is finally there with LEDs, where you can get excellent daylight- and incandescent-quality lighting at significantly reduced costs,” Taeger explains. Not only do the LEDs offer dramatic energy savings, but Plaza Tower tenants never have to worry about reporting burned-out lights. Once the LEDs are in place, they typically don’t need to be touched for 15 to 20 years. This helps cut down on maintenance and labor expenses as well.
Daily routine maintenance for the tower’s dual elevator banks also decreases tenant complaints and calls to report out-of-order elevators. “When you get into the Plaza Tower elevators, you can stand a nickel up on its end, ride up to the top floor and back down, and the nickel won’t fall over,” Lambert says. “I can’t think of any other building where the elevators run that smoothly.”
This dedication to quality and maintenance is evident throughout the building, and is possible thanks to owner C.J. Segerstrom & Sons’ approach, says Lambert. “They’ve owned the building since it was built, and they maintain it as if they’re going to own it forever. Everything is done with the long-term in mind.”
Plaza Tower also participates in Orange County’s Green Acres Project, a water recycling program that provides reclaimed water for landscape irrigation at parks, schools, and golf courses, as well as for industrial uses. As one of the few commercial development participants, the building benefits from using recycled water irrigation for outdoor areas and landscaping. To further encourage water savings, every toilet and urinal in the building has been replaced with more efficient, low-flow models.
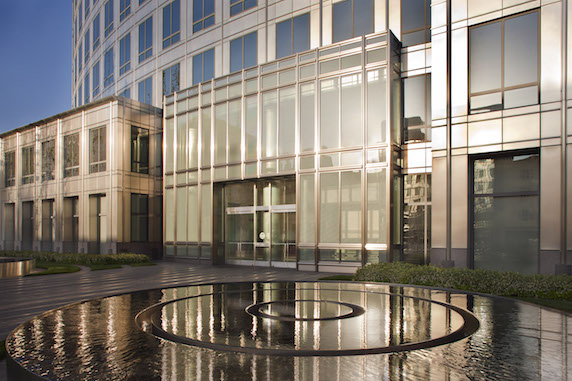
Even though the building is 23 years old, Plaza Tower’s operations are better than the majority of buildings being built today. All of the building’s upgrades were done without raising operating expenses.
Little Changes, Big Impact
After making some adjustments to what is considered recyclable at Plaza Tower (and investing in larger recycling compactors), more than 70 percent of the building’s trash is now recycled. All carpet and other building materials are also recycled whenever construction or renovation projects occur.
The janitorial company follows green cleaning practices, and Plaza Tower was the first to incorporate microfiber cloths as part of its overall cleaning and maintenance program.
Alternative energy sources, including solar and wind power, are purchased for the building, which can offer protection against power market volatility while reducing carbon emissions.
The building also invests in annual indoor air quality (IAQ) surveys to make sure the indoor air is as good as possible. If this isn’t indicated in the test results, then improvements are made accordingly. The IAQ survey findings are shared with tenants so they can be confident about the air they breathe.
Making a Good Thing Even Better
“LEED is an excellent way to help us show that Plaza Tower is as good as – or better than – any other building in the marketplace,” Taeger emphasizes. “But this doesn’t mean that we don’t continue to improve. Even though we’ve earned Platinum certification, we’re always discussing how we can further advance operations. It’s all about creating a product that is more competitive.”
Even though the building is 23 years old, Taeger and Lambert say the LEED-EB: O&M Platinum status proves that Plaza Tower’s operations are better than the majority of buildings being built today. And all of the building’s changes and improvements have been done without raising operating expenses.
The LEED-EB: O&M Platinum certification has also helped Plaza Tower tenants attract and retain talent. “The brightest young attorneys want to work in a building that’s not only good for the environment, but that’s a healthy place to work,” says Lambert. “We’ve entered that phase in the job market where it’s hard to find employees again. Rather than focusing on cost-cutting, tenants are instead focused on employee recruiting and attracting. They’re willing to make the commitment to be in better buildings in order to improve attraction and retention rates.”
Leah Grout Garris
An award winning editor, Leah spent over eight years in senior
editorial positions at both BUILDINGS magazine and ARCHI-TECH
magazine. Her work has been incorporated into training and
educational programs around the country. She is a graduate of
University of Iowa. She is Editor at Large for High Rise Facilities.